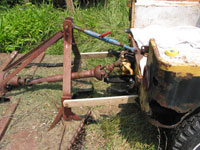
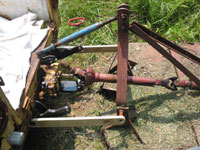
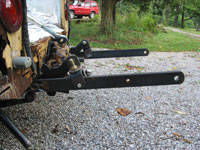
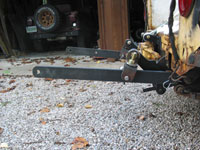
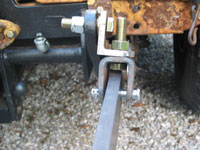
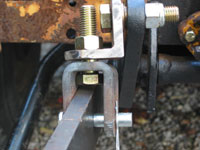
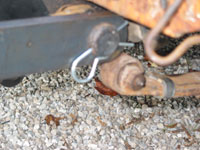
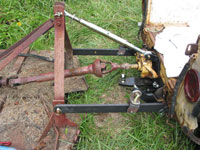
|
|
Up
in Arms
It has been almost a year since we acquired the Newgren lift. We have
continued to search for the missing implement arms and linkage, but
haven’t been able to do better than a few pictures. Rather than
wait, we decided to fabricate a set of arms, based on the documentation
available.
Measure twice
The arms are actually very simple. Unlike most tractor arms, they don’t
have knuckles (ball joints) on the ends. They are a simple metal bar
with three holes. The linkage between the short lift arms and the implement
arms was more complicated. In the end, we used a simplified linkage
approach for now.
We first created wooden models, since we were going to have to have
the metal bars made by a local welding shop. We based the length on
the pictures we had and by attempting to scale the drawings included
in the mounting instructions. Our test equipment was a bush hog, which
would involve the PTO in addition to the lift. As can be seen from the
picture, the arms were too short to allow the PTO hook up. This was
a simple fix at this stage; we built a second set of wooden arms, adding
6” to the length.
Barry took one of the wooden arms as a pattern to his local welder.
He also took copies of the pictures we had of the linkage. The building
took a couple of weeks, and involved ordering the steel bar (3/4”)
and sending the arms to a machine shape to have the large holes drilled.
The machine shop broke a couple of bits and it delayed the process by
a week. But the end product turned out well and the arms fit perfectly.
The linkage presented more of a challenge for the welding shop. In the
end, they simply made an “L” shaped hanger and forged “U”
brackets to attach to the implement arm. We are using ¾”
grade 8 bolts to hold everything together.
Topping it off
While the arms where being made, Barry tackled the problem of the top
link (the third point of the three point hitch) The pictures seem to
show a two-part steel bar, with holes allowing for length adjustments.
From a practical standpoint, this was a much inferior design to the
more common screw-type top link. We may replicate the adjustable bar
for show purposes, but for doing actual work, we will use a standard
screw-type bar.
The top link on the Newgren is not as wide as those on modern tractors.
Barry had to grind the “ears” off of the knuckle on one
end of a store-bought link. It fits perfectly and allows for easy adjustments
when mounting implements. That is a trait not shared by the implement
arms.
The don’t make’em like that any more
When Barry finally picked up the arms, he couldn’t wait to try
them out. The arms are very heavy; ¾” steel bars, 2 ½”
wide and 30” long. The hangers are simple and still allow for
height adjustments by raising or lowering the nuts. Everything fit perfectly
and went together with a few bolts and pins.
Although not clear from the drawing or pictures, it appears that a bushing
was used in the hole of the small lift arm. The holes where either cut
to the rough dimension or have wear. In either case we felt a bushing
was needed and are using a bronze type found at the local hardware store.
The hole thing
Once assembled, Barry
drove the jeep out to meet the bush hog. He had several observations.
First, while it is easy to see out the back, the lack of power steering
makes aligning the lift and implement a challenge. Second, on a tractor,
those knuckles on the end of the implement arm are forgiving; they allow
you to slide the arm on even when not perfectly aligned. Not so with
solid ¾” bars with holes just large enough to accept the
implement pins. The Newgren method requires pulling, tugging and lots
of swearing. This is going to take practice.
Much to his dismay, Barry discovered that one of the holes had been
drilled to small. It was an 1/8” off. Back to the house and into
town for a 7/8” drill bit to finish the job. But Barry did have
enough evidence that the arms where the right length and that the thing
might actually work.
Mower than we bargained for
A day and $10 (the cost of the bit) later, Barry tried mounting the
bush hog again. After much backing, pulling forward, swearing and backing
again, he got the arms on the bush hog and the top link attached. Now
for the test. He pulled the control to raise the lift and … Squat.
That is what the jeep did, but the bush hog wouldn’t come off
the ground. Granted, this is the heaviest 3-point implement we own,
but the Newgren should be able to lift it off the ground. More work
is needed on the pump.
Going with the flow
Evan was able to come down for some more testing. Based on the advice
of the chief mechanics, he added more fluid to the reservoir. He rode
up and down on the arms a few times and declared it ready for another
test.
This time the target was a plow. This plow a “2-14s” is
bigger and heavier than the recommend “2-12s” but should
be good for testing. Evan did the driving and Barry did the directing.
It was clear that two people make the job of implement mounting much
easier. With more tugging, the plow was mounted. Evan hit the lift switch
and the plow came up – but just a little.
We disconnected the between-seats control lever to ensure we weren’t
limiting the valve travel. It helped a little (we will need to adjust
the forward rod when this is all working), but still not a full lift.
Back to the garage for more fluid and load testing. We both stood on
the rear arms and worked the pump. One more time to the field and this
time some success. However, it was clear that we have too much linkage
space between the lift and implement arms. We could gain a couple of
inches in height by flipping the “L” brackets over.
One more trip to the garage. The simple design of the linkage made the
change easy. We replace the bolts with slightly (1”) longer versions
and headed back out to the field. This time the target was an old carry-all.
More tugging and pulling to get the carry-all mounted, but the lift
worked better.
That doesn’t sound right
The lift valve is making lots of noise when under load. Although the
instructions say “no adjustment need to the factory settings”
it may be that 50 years of rust and dirt have taken their toll. More
bleeding and cleaning seem to be in order and the underbody design makes
it hard to get at the parts. We may just live with the slow lift for
now and are seeking professional advice on next steps.
But at the end of the day, we have a real live working Farm Jeep!
Barry’s notes:
Lots of lessons learned here. First, I still like the Newgren basic
design. The arms come off by pulling four pins and are out of the way
when not in use. Second the Newgren arm design makes single person implement
mounting tough. I think I may make a second set of arms with knuckles
on end. Too much pulling and tugging required with the real thing. They
will be nice for shows (someday) and I don’t regret going this
route.
Evan’s notes:
|
|